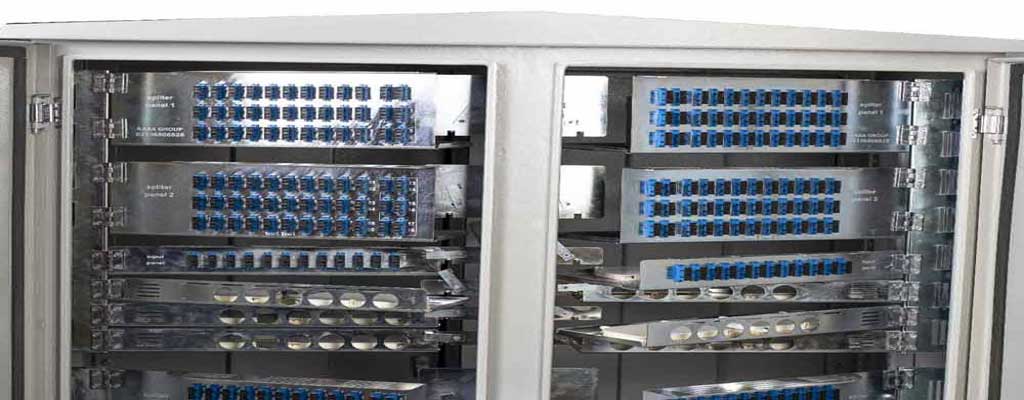
دستور العمل عملیات رنگ و شستشو رک ها و باکسهای فلزی
1 –هدف :
هدف از تدوین این دستورالعمل معین نمودن نحوه انجام کار در قسمت رنگ و کنترل کیفیت در این قسمت می باشد.
2- دامنه کاربرد :
این دستورالعمل برای قسمت رنگ گروه مهندسی رسا صنعت آپادانا کاربرد دارد.
3- مسئولیت ها :
مسئولیت اجرای این دستورالعمل با مدیر تولید بوده و کلیه افراد شاغل درقسمت رنگ موظف به رعایت کلیه نکات آن می باشند.
4- شرح عملیات :
4-1 آماده سازی وانهای شست و شو :
4-1-1- بر اساس دستورالعمل کارخانه سازنده مواد شست و شو وانها شارژ و جهت انجام عملیات آماده خواهد شد.
4-2 کنترل کیفیت وانهای شست و شو :
4-2-1-وانها قبل از شروع کار توسط اپراتور از نظر دما و میزان مواد براساس دستور العمل های فوق کنترل و شارژ خواهد گردید.
4-2-2- جهت شارژ مجدد وانها پس از انجام تیتراسیون با توجه به فرم کنترل وانهای شستشو به کد QC-FO-10 مواد مورد نیاز مشخص می گردد، که اپراتور خط موظف به شارژ با هماهنگی کنترل کیفیت می باشد.
4-3 آماده سازی قطعات
قطعات تحویلی از فلزکاری از نظر ظاهری کنترل گردیده و پس از اطمینان از تمیز کاری مناسب و زنگ بری و تمیز کردن آلودگی های سطحی در سبد شست و شو گذاشته شده، توسط جرثقیل به وان چربیگیر انتقال می گردد.
4-4 چربیگیری
قطعات منتقل شده در وان چربیگیر در مدت زمان و دمای تعیین شده در وان قرار خواهد گرفت و پس از آن به وسیله جرثقیل به وان آب کش منتقل می گردد. مدت زمان قرار گیری در وان آب کش در حد یک لحظه بوده و پس از بالا آوردن از وان و اطمینان از چربیگیری مناسب به وان فسفاته منتقل خواهد شد.
4-5 عملیات فسفاته
قطعات منتقل شده در وان فسفاته در مدت زمان و دمای تعیین شده در وان قرار خواهد گرفت و پس از آن به وسیله جرثقیل به وان آب کش منتقل می گردد .مدت زمان قرار گیری در وان آب کش در حد یک لحظه بوده و پس از بالا آوردن از وان به قسمت خشک کن منتقل خواهد شد.
4-6 کنترل کیفیت شست و شو قطعات
4-6-1 – کنترل کیفیت وانها
وانها قبل از شروع عملیات شستشو از نظر میزان مواد و دما باید کنترل گردد.
4-6-2- کنترل در حین انجام عملیات شستشو
در حین انجام مراحل شستشو وانها از نظر زمان، دما و قطعات ازنظر اطمینان از چربی گیری مناسب باید کنترل گردند.
4-6-3- کنترل پس از اتمام عملیات شستشو
پس از اتمام کار و خشک شدن، قطعات از نظر نداشتن زنگ، چربی و فسفاته مناسب، باید کنترل و تایید گردند از این مرحله به بعد دست گذاشتن به قطعات ممنوع بوده و باید حمل و نقل با دستکش تمیز انجام پذیرد حداکثر زمان جهت رنگ قطعات 24 ساعت می باشد و در صورت عدم امکان رنگ در زمان قید شده باید بوسیله نایلون تمیز جهت پیشگیری از نشست گرد و خاک محافظت گردد.
4-6-4- تکمیل شناسنامه قطعات
پس از اتمام کار شستشو و اطمینان از صحت عملیات فرم شناسنامه ساخت قطعات در فلزکاری و رنگ به کد فرم PR.FO.03 توسط اپراتور تکمیل می گردد.
4-7- رنگ
4-7-1 پاشش رنگ :
قطعات پس از انتقال به اتاق پاشش رنگ خواهد گردید، رنگ مورد استفاده در این قسمت از نوع پودری الکترواستاتیک بوده و حالت جامد دارد لذا با توجه به پروسه باید قبل از اقدام به رنگ اتصال کلیه تجهیزات با ارت کنترل گردد و پس از پاشش در صورت برخورد دست رنگ در محل برخورد جدا خواهد شد.
4-7-2 پخت رنگ :
کوره قبل از ورود قطعات روشن و پس از رسیدن به دمای پخت خاموش خواهد شد. قطعات پس از رنگ به کوره منتقل و بعد از بستن در و گذشت 5 دقیقه مجدداً روشن خواهد گردید، مدت زمان و درجه پخت رنگ بر اسا س دستورالعمل سازنده می باشد. پس از پخت رنگ قطعات بیرون آورده شده و بعد از سرد شدن از نظر پوشش کامل و ضخامت مطابق دستور ساخت کنترل خواهد گردید و در صورت تایید به قسمت مونتاژ و قطعات رنگ شده منتقل می گردد.
4-7-3- تکمیل شناسنامه قطعات
پس از اتمام کار رنگ و اطمینان از صحت رنگ فرم شناسنامه ساخت قطعات در فلزکاری و رنگ به کد فرم PR.FO.03 توسط اپراتور تکمیل می گردد.
4-7-3 تست رنگ:
4-7-3-1 ضخامت سنجی
قطعات رنگ شده پس از اعمال رنگ و پخت از نظر ضخامت با دستگاه ضخامت سنج کنترل شده و در صورت قرار داشتن ضخامت رنگ در رنج مورد نظر، حداقل و حداکثر ضخامت بر اساس میکرون در فرم شناسنامه ساخت قطعات در فلزکاری و رنگ به کد فرم PR.FO.03 قطعه قید می گردد.
تبصره 1: دستگاه ضخامت سنج باید قبل از کار با فیلمهای تست موجود کنترل و از نظر نقطه صفر و رنج ضخامت مورد استفاده کنترل گردد و در صورت مغایرت ابتدا کالیبره شده سپس مورد استفاده قرار گیرد.
تبصره 2: میانگین ضخامت قید شده در شرایط عادی 80 میکرومتر بوده که حداقل آن نباید از 50 میکرومتر کمتر باشد.
تبصره3: در شرایطی که مشتری طبق قرارداد ضخامت دیگری در رابطه با رنگ درخواست نماید ضخامت مورد نظر باید از طریق مدیر تولید به اپراتور رنگ و کنترلر خط اعلام گردد.
4-7-3-2 تست چسبندگی :
این تست باتوجه به ماهیت مخرب بودن آن امکان انجام روی قطعات اصلی را ندارد ، لذا در مواقع مورد نیاز باید روی قطعاتی که جهت این تست شستشو و رنگ گردیده است اجرا گردد.
ابتدا بوسیله کراس کاتر به شیوه ای روی رنگ خراش ایجاد می گردد که از رسیدن خراشها به سطح فلز اطمینان حاصل گردد. این خراشها به صورت دو ردیف خراش عمود بر هم خواهد بود.
سپس بوسیله برس سطح مورد نظر به شیوه ای تمیز خواهد گردید که سطح کاملاً از ذره های حاصل از ایجاد خراش تمیز گردد ، سپس چسب مخصوص روی سطح چسبانده شده و پس از گذشت زمان ماند، از روی قطعه جدا خواهد شد، مقایسه سطح خراش با جدول زیر وضعیت چسبندگی رنگ را تعیین خواهد نمود.
4-7-3-3تست مه نمکی (Salt Spray):
بسیاری از محصولات فلزی به دلیل کاربردشان در شرایط خاص باید از لحاظ مقاومت در برابر خوردگی تحت آزمون قرار گیرند.
آزمون سالت اسپری، یک روش آزمون استاندارد برای ارزیابی میزان خوردگی فلزات رنگ خورده و پوشیده شده است. پوشش و رنگ ها موجب مقاومت در برابر خوردگی قطعات فلزی می شود. سالت اسپری یک دستگاه ایجاد شرایط خوردگی تسریع شده برای نمونه های پوشش داده شده و یا رنگ شده می باشد. تا ازاین طریق میزان حفاظت سطح پوشش در برابر خوردگی مورد بررسی قرار گیرد.
این شرایط شامل یک محیط خاص رطوبتی می باشد.در این محیط علاوه بر رطوبت اشباع، محلولی از آب و نمک موجود می باشد.
ایجاد این شرایط برای نمونه باعث مشابه شدن مکان استفاده بعضی از محصولات، البته با کم کردن زمان و افزایش شدت مواد تأثیر گذار بر روی آن ها می باشد، که بدین ترتیب نمونه را از لحاظ مقاومت در برابر خوردگی مورد بررسی قرار می دهند.
در این آزمون نمونه مورد نظر در یک محفظه ی رطوبتی قرار می گیرد. در این محفظه علاوه بر رطوبت یک اسپری، محلول آب نمک را بر روی نمونه می پاشد .
این آزمون با توجه به عدم وجود دستگاه و تجهیزات آن در شرکت، برون سپاری خواهد شد. و حداقل سالی یکبار توسط موسسات معتبر روی فیلمهایی که ابعاد آن توسط موسسه انجام دهنده تعیین خواهد شد، انجام خواهد گرفت ابتدا یک عدد قطعه تهیه و بر اساس شرایط واقعی خط شستشو و رنگ خواهد شد، سپس جهت انجام تست ارسال خواهد شد و پس از دریافت جواب در صورت تایید نتایج آن نگهداری خواهد شد و در صورت عدم تایید و شروع خوردگی رنگ قبل از زمان مورد نظر ایرادات خط بررسی و مجدداً تست تکرار خواهد شد. در شرایط تغییر پروسه تولید، نوع رنگ و یا درخواست مشتری این تست زود تر از موعد انجام خواهد گرفت.
تعداد نظرات داده شده برای این خبر:۰